We continue the action this week with a look at Volvo Trucks' VR training rollouts. It was able to scale VR across its training operations and now wants to take it even further. How did it do this and what did it learn?
Key Takeaways & Analysis– It's no secret that immersive training is an enterprise VR's top use case.
– Among other things, it's cheaper and safer to train in simulated environments.
– And its levels of immersion support visceral and experiential learning.
– All of this applies to auto manufacturers, amplified by scale and high stakes.
– Volvo saw even greater benefits to train mechanics for its electric freight trucks.
– The amount of electricity in play makes these trucks unsafe to fix.
– And that safety risk is multiplied for novice mechanics... in other words, trainees.
– Beyond safety, Volvo was able to lower costs due to mass travel for training pros.
– There are also speed benefits, such as resetting training sequences in seconds.
– Analog training methods required time to reset sequences for the next trainee.
– But the rollout wasn't without challenges, such as overcoming motion sickness.
– Volvo alleviated this by shortening training sessions to 30 minutes at a time.
– Altogether the VR training program was a success on several levels.
– For example, it achieved tangible productivity boosts and cost savings.
– It was also highly rated by trainees, which is important to ensure they're engaged.
– The program's success caused Volvo to look for other functions to apply VR.
– Going forward, it's bringing VR to sales training and leadership training.
– It also wants to integrate AI to automate and fill gaps in training resources.
– AI has already helped localize training by translating courses for different regions.
For more color, see the full video below...
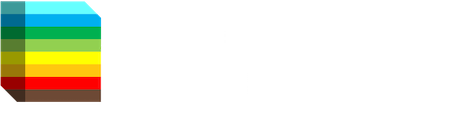
Want more XR insights and multimedia? ARtillery Intelligence offers an indexed and searchable library of XR intelligence known as ARtillery Pro. See more here.